JIT-打造準時化生產體系
2022-08-12 15:12:40 來源:郭濤 點擊:
JIT-打造準時化生產體系【課程背景】精益生產(LeanProduction,簡稱LP)是因為日本汽車業(yè)本世紀在世界崛起,美國麻省理工學院根據(jù)其在國際汽車項目研究中,基于對日本豐田生產方式(Toyota Production System)
JIT-打造準時化生產體系
【課程背景】
精益生產(LeanProduction,簡稱LP)是因為日本汽車業(yè)本世紀在世界崛起,美國麻省理工學院根據(jù)其在“國際汽車項目”研究中,基于對日本豐田生產方式(Toyota Production System)的研究與總結,以及對美國汽車工業(yè)的反思與總結,提出的一種生產管理方法。
“歐美企業(yè)將三分之二的研究發(fā)展經(jīng)費,花在新產品研發(fā)上面,將另外三分之一的錢用在生產過程的改善;可是日本的做法剛好相反。而我認為歐美的做法是錯誤的,以前,發(fā)明、開發(fā)新產品是企業(yè)競爭中最重要的武器,但是現(xiàn)在競賽的重心是在于生產過程的改善。”
——美國麻省理工學院管理學院院長梭羅教授。
精益生產技術就是改善生產過程的最佳利器,采用了精益生產技術的日本豐田汽車公司,2003與04年連續(xù)兩個年度營業(yè)利潤均達到美國三大汽車公司(通用、福特、克萊斯勒)利潤總和的6~7倍,這是因為精益生產的改善,能夠同時達成品質、成本、交期、服務、士氣的改善。
【授課對象】生產總經(jīng)理、副總經(jīng)理、生產總監(jiān)/廠長,供應鏈總監(jiān)、精益/生產經(jīng)理、物流經(jīng)理
【課程價值】
u 認識 “高質量、低成本、短交期”和“持續(xù)改善”的精益生產核心理念;
u 掌握企業(yè)競爭的兩大要素與企業(yè)經(jīng)營的三種理念
u 掌握企業(yè)現(xiàn)場浪費之源與八大浪費,并持續(xù)消除浪費;
u 掌握生產線布局的思路,方法,工具與實施八步驟
u 掌握標準作業(yè)的“三件套”表單制定的思路與方法
u 掌握多能工培訓的“四字訣“與培訓的四步驟
u 掌握設備綜合效率的計算方法與OEE提升思路
u 掌握快速切換在精益生產中的作用與快速切換的七步驟
u 掌握自工程完結的三要素與實施的八步法
u 掌握現(xiàn)場5S實施要點與目視化管理的三級水平
u 掌握準時化生產的條件與看板拉動的運作方法
【工具/表單】
l 物流布局圖 / 生產計劃流程圖 / 浪費地圖 / 價值流程圖 / “三不“模型
l 浪費識別表 / 物料清單表 / 標準作業(yè)表 / 多能工表 / 員工技能表
【課程特色】45%理論+35%案例講解+15%現(xiàn)場演練+5%點評總結
【課程時長】2天/12H
【課綱內容】
第一講:精益生產概論
一、企業(yè)競爭的兩大要素
視頻案例分析:從國慶閱兵看精益生產
二、精益生產發(fā)展的歷史
三、企業(yè)永續(xù)經(jīng)營的根本
四、企業(yè)經(jīng)營的三種理念
五、精益生產的五大原則
六、價值—價值流—流動—拉動—盡善盡美
案例分析:多伊爾.威爾遜案例
七、企業(yè)常見的七大浪費
視頻案例:烤面包
課堂演練:尋找浪費
第二講:精益生產管理之生產線設計
一、流線化生產的目的
1、工廠常見的布局類型
2、集中式生產布局
二、流線化生產與批量生產的區(qū)別
案例分析:單件流與批量流
三、流線化生產幾種類型
四、流線化生產線設計
1、定義產品簇
2、P/Q與P/R分析
3、VSM現(xiàn)狀圖繪制
4、VSM未來圖繪制
案例分享:某產品現(xiàn)狀圖與未來圖
五、流線化設計的幾大要素
1、物流要素:
2、人員要素
3、設備要素
視頻案例分析:某日企業(yè)流線化視頻案例
六、流線化生產線建立步驟
七、一筆畫工廠布置
第三講:精益生產管理之人員安定
視頻案例:某企業(yè)標準作業(yè)
一、標準作業(yè)與作業(yè)標準的區(qū)別
二、標準作業(yè)的三條件與三要素
三、標準作業(yè)的作成步驟
現(xiàn)場演練:標準作業(yè)票作成
四、實施標準作業(yè)改善的步驟
1、改善的步驟
2、如何從標準作業(yè)“三件套”找問題
3、運用動作經(jīng)濟原則改善
五、多能工培養(yǎng)與管理
1、多能工培養(yǎng)之“選“—選工序與選擇人
2、多能工培養(yǎng)之“訓“—教導四步法
3、多能工培養(yǎng)之“評“—理論與績效
4、多能工培養(yǎng)之“用“—變更管理
案例分享:某日資企業(yè)多能工培養(yǎng)與管理案例
六、生產線平衡
案例分享:某企業(yè)線平衡案例
現(xiàn)場演練:線平衡率提升
第四講:精益生產管理之設備安定
一、設備效率的三大指標
二、設備效率之OEE提升
案例演練:OEE計算
案例分享:某企業(yè)OEE效率提升案例
三、設備效率之點檢效率提升
1、“三位一體“點檢制與五層防護線機制構建
2、年度—季度—月度—周—日點檢體系構建
3、設備點檢管理四大標準構建
案例分析:某企業(yè)設備點檢四大標準表
案例分析:某日企設備目視化體系案例
4、點檢操作實施三級階
案例分析:某企業(yè)點檢員的一日工作
四、設備效率之故障解決效率提升
1、 設備故障管理的主要內容
2、 零故障的五大對策與TPM五大支柱關系
3、 設備故障管理的三大工具-流程/記錄/報告
案例分享:某日資企業(yè)故障解決實施案例
第五講:精益生產管理之切換安定
一、為什么要實施快速切換
視頻案例分析:F1換輪胎
案例討論:快速切換對生產周期有什么影響
二、快速換模分析
三、減少切換的改善順序
1、準備更換損失時間的實際狀況調查
2、高層領導的態(tài)度表明和項目組的組成
3、現(xiàn)場觀察和連續(xù)稼動分析
4、把切換結果整理為三種浪費分析
1、 全員參與的改善實施計劃制定
6、改善實施,評價與推廣
四、實現(xiàn)快速換模的七步法
案例分享:某日企注塑模具切換案例
五、快速切換八大法則
第六講:精益生產管理之品質安定
一、制造質量概述
案例分享:某企業(yè)自工序完結案例分享
二、自工序完結的三大要素
案例分享:某臺企自工程完成的案例
三、自工序完結管理機制構架圖
1、 技術面
2、 作業(yè)面
3、 管理面
四、自工序完結的重點實施事項
1、 區(qū)分自工序完結的不同層次
2、 用自工序完結管理板實行目視化
案例分析:某企業(yè)自工序完結看板
五、工序完結職責—輔助部門與員工的職任
六、自工序完結的推進方法
七、自工序完結實施方案
案例分享:自工序完結案例分享
第七講:精益生產管理之現(xiàn)場安定化
一、現(xiàn)場安定的前提—問題無處藏身
二、現(xiàn)場安定的基礎—整理,整頓
1、 整理推行要領—清理/清除/清爽
2、 整頓推行要領—場所/方法/標識
視頻案例分析:歷史轉折中的鄧小平片段
三、目視化管理的三大階段
四、現(xiàn)場安定之對象—人/機/料/法/環(huán)
案例分享:日企現(xiàn)場目視化案例
第八講:精益生產管理之準時化
一、傳統(tǒng)生產方式與JIT方式的比較
二、準時化的前提條件—均衡化排產
三、幾種常見的準時化生產方式
1、順序拉動系統(tǒng)
2、后工序拉動系統(tǒng)
1、 混合拉動系統(tǒng)
四、實現(xiàn)準時化生產的條件
1、 看板拉動如何實現(xiàn)
2、實施看板的前提條件
視頻案例分析:波音777生產線
2、 看板系統(tǒng)設計與使用
1、 看板的種類與用途
2、 看板系統(tǒng)設計思路
3、 看板運轉六大紀律
4、 看板拉動系統(tǒng)
視頻案例分享:某汽車廠拉動生產視頻
現(xiàn)場模擬演練:折紙飛機
總結,答疑!
【課程背景】
精益生產(LeanProduction,簡稱LP)是因為日本汽車業(yè)本世紀在世界崛起,美國麻省理工學院根據(jù)其在“國際汽車項目”研究中,基于對日本豐田生產方式(Toyota Production System)的研究與總結,以及對美國汽車工業(yè)的反思與總結,提出的一種生產管理方法。
“歐美企業(yè)將三分之二的研究發(fā)展經(jīng)費,花在新產品研發(fā)上面,將另外三分之一的錢用在生產過程的改善;可是日本的做法剛好相反。而我認為歐美的做法是錯誤的,以前,發(fā)明、開發(fā)新產品是企業(yè)競爭中最重要的武器,但是現(xiàn)在競賽的重心是在于生產過程的改善。”
——美國麻省理工學院管理學院院長梭羅教授。
精益生產技術就是改善生產過程的最佳利器,采用了精益生產技術的日本豐田汽車公司,2003與04年連續(xù)兩個年度營業(yè)利潤均達到美國三大汽車公司(通用、福特、克萊斯勒)利潤總和的6~7倍,這是因為精益生產的改善,能夠同時達成品質、成本、交期、服務、士氣的改善。
【授課對象】生產總經(jīng)理、副總經(jīng)理、生產總監(jiān)/廠長,供應鏈總監(jiān)、精益/生產經(jīng)理、物流經(jīng)理
【課程價值】
u 認識 “高質量、低成本、短交期”和“持續(xù)改善”的精益生產核心理念;
u 掌握企業(yè)競爭的兩大要素與企業(yè)經(jīng)營的三種理念
u 掌握企業(yè)現(xiàn)場浪費之源與八大浪費,并持續(xù)消除浪費;
u 掌握生產線布局的思路,方法,工具與實施八步驟
u 掌握標準作業(yè)的“三件套”表單制定的思路與方法
u 掌握多能工培訓的“四字訣“與培訓的四步驟
u 掌握設備綜合效率的計算方法與OEE提升思路
u 掌握快速切換在精益生產中的作用與快速切換的七步驟
u 掌握自工程完結的三要素與實施的八步法
u 掌握現(xiàn)場5S實施要點與目視化管理的三級水平
u 掌握準時化生產的條件與看板拉動的運作方法
【工具/表單】
l 物流布局圖 / 生產計劃流程圖 / 浪費地圖 / 價值流程圖 / “三不“模型
l 浪費識別表 / 物料清單表 / 標準作業(yè)表 / 多能工表 / 員工技能表
【課程特色】45%理論+35%案例講解+15%現(xiàn)場演練+5%點評總結
【課程時長】2天/12H
【課綱內容】
第一講:精益生產概論
一、企業(yè)競爭的兩大要素
視頻案例分析:從國慶閱兵看精益生產
二、精益生產發(fā)展的歷史
三、企業(yè)永續(xù)經(jīng)營的根本
四、企業(yè)經(jīng)營的三種理念
五、精益生產的五大原則
六、價值—價值流—流動—拉動—盡善盡美
案例分析:多伊爾.威爾遜案例
七、企業(yè)常見的七大浪費
視頻案例:烤面包
課堂演練:尋找浪費
第二講:精益生產管理之生產線設計
一、流線化生產的目的
1、工廠常見的布局類型
2、集中式生產布局
二、流線化生產與批量生產的區(qū)別
案例分析:單件流與批量流
三、流線化生產幾種類型
四、流線化生產線設計
1、定義產品簇
2、P/Q與P/R分析
3、VSM現(xiàn)狀圖繪制
4、VSM未來圖繪制
案例分享:某產品現(xiàn)狀圖與未來圖
五、流線化設計的幾大要素
1、物流要素:
2、人員要素
3、設備要素
視頻案例分析:某日企業(yè)流線化視頻案例
六、流線化生產線建立步驟
七、一筆畫工廠布置
第三講:精益生產管理之人員安定
視頻案例:某企業(yè)標準作業(yè)
一、標準作業(yè)與作業(yè)標準的區(qū)別
二、標準作業(yè)的三條件與三要素
三、標準作業(yè)的作成步驟
現(xiàn)場演練:標準作業(yè)票作成
四、實施標準作業(yè)改善的步驟
1、改善的步驟
2、如何從標準作業(yè)“三件套”找問題
3、運用動作經(jīng)濟原則改善
五、多能工培養(yǎng)與管理
1、多能工培養(yǎng)之“選“—選工序與選擇人
2、多能工培養(yǎng)之“訓“—教導四步法
3、多能工培養(yǎng)之“評“—理論與績效
4、多能工培養(yǎng)之“用“—變更管理
案例分享:某日資企業(yè)多能工培養(yǎng)與管理案例
六、生產線平衡
案例分享:某企業(yè)線平衡案例
現(xiàn)場演練:線平衡率提升
第四講:精益生產管理之設備安定
一、設備效率的三大指標
二、設備效率之OEE提升
案例演練:OEE計算
案例分享:某企業(yè)OEE效率提升案例
三、設備效率之點檢效率提升
1、“三位一體“點檢制與五層防護線機制構建
2、年度—季度—月度—周—日點檢體系構建
3、設備點檢管理四大標準構建
案例分析:某企業(yè)設備點檢四大標準表
案例分析:某日企設備目視化體系案例
4、點檢操作實施三級階
案例分析:某企業(yè)點檢員的一日工作
四、設備效率之故障解決效率提升
1、 設備故障管理的主要內容
2、 零故障的五大對策與TPM五大支柱關系
3、 設備故障管理的三大工具-流程/記錄/報告
案例分享:某日資企業(yè)故障解決實施案例
第五講:精益生產管理之切換安定
一、為什么要實施快速切換
視頻案例分析:F1換輪胎
案例討論:快速切換對生產周期有什么影響
二、快速換模分析
三、減少切換的改善順序
1、準備更換損失時間的實際狀況調查
2、高層領導的態(tài)度表明和項目組的組成
3、現(xiàn)場觀察和連續(xù)稼動分析
4、把切換結果整理為三種浪費分析
1、 全員參與的改善實施計劃制定
6、改善實施,評價與推廣
四、實現(xiàn)快速換模的七步法
案例分享:某日企注塑模具切換案例
五、快速切換八大法則
第六講:精益生產管理之品質安定
一、制造質量概述
案例分享:某企業(yè)自工序完結案例分享
二、自工序完結的三大要素
案例分享:某臺企自工程完成的案例
三、自工序完結管理機制構架圖
1、 技術面
2、 作業(yè)面
3、 管理面
四、自工序完結的重點實施事項
1、 區(qū)分自工序完結的不同層次
2、 用自工序完結管理板實行目視化
案例分析:某企業(yè)自工序完結看板
五、工序完結職責—輔助部門與員工的職任
六、自工序完結的推進方法
七、自工序完結實施方案
案例分享:自工序完結案例分享
第七講:精益生產管理之現(xiàn)場安定化
一、現(xiàn)場安定的前提—問題無處藏身
二、現(xiàn)場安定的基礎—整理,整頓
1、 整理推行要領—清理/清除/清爽
2、 整頓推行要領—場所/方法/標識
視頻案例分析:歷史轉折中的鄧小平片段
三、目視化管理的三大階段
四、現(xiàn)場安定之對象—人/機/料/法/環(huán)
案例分享:日企現(xiàn)場目視化案例
第八講:精益生產管理之準時化
一、傳統(tǒng)生產方式與JIT方式的比較
二、準時化的前提條件—均衡化排產
三、幾種常見的準時化生產方式
1、順序拉動系統(tǒng)
2、后工序拉動系統(tǒng)
1、 混合拉動系統(tǒng)
四、實現(xiàn)準時化生產的條件
1、 看板拉動如何實現(xiàn)
2、實施看板的前提條件
視頻案例分析:波音777生產線
2、 看板系統(tǒng)設計與使用
1、 看板的種類與用途
2、 看板系統(tǒng)設計思路
3、 看板運轉六大紀律
4、 看板拉動系統(tǒng)
視頻案例分享:某汽車廠拉動生產視頻
現(xiàn)場模擬演練:折紙飛機
總結,答疑!
上一篇:對標奔馳班組建設與管理
下一篇:精益管理業(yè)務流程改善培訓
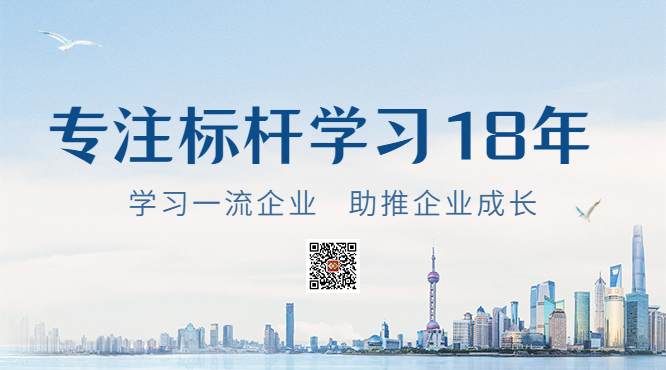
考察研學聯(lián)系方式/參觀預約申請
- 聯(lián)系電話:010-52463211
- 聯(lián)系手機:13661395399
- 聯(lián)系人:萬斌老師
考察公開課推薦
- 2025年公開課考察計劃
- 2025年11月24-25日 對標阿里巴巴&抖音&網(wǎng)易 學企業(yè)出海營銷實戰(zhàn)
- 2025年8月21-22日 考察領軍企業(yè)出海秘籍 對標華為、聯(lián)想、傳音 出海實戰(zhàn)案例
- 2025年5月12-13日 中國企業(yè)出海營銷的制勝之道 考察美的、名創(chuàng)優(yōu)品、希音
- 2025年7月12-13日 北京專場 對標華為、騰訊、京東 學HRBP如何為業(yè)務創(chuàng)造價值
- 2025年3月28-29日 上海專場 對標華為、騰訊學HRBP如何為業(yè)務創(chuàng)造價值
- 2025年2月21-22日 深圳專場 對標華為、騰訊學HRBP如何為業(yè)務創(chuàng)造價值
- 2025年4月21-22日 揭秘品牌背后的創(chuàng)新營銷密碼 對標小紅書、抖音、瑞幸咖啡、東鵬特飲
- 5月19-20日 對標上海星巴克、東鵬特飲、霸王茶姬、泰山原漿 學習智慧零售打造
- 2025年4月28-29日 走進北京阿里&智譜&京東&華為 對標AI賦能企業(yè)增長的新紀元